News Story
Understanding the Flammability of Charring Polymers
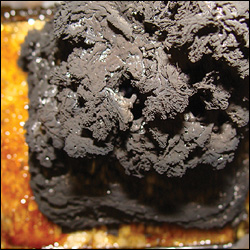
A charred sample of Bisphenol A (BPA) polycarbonate. The orange surface is non-degraded or partially degraded polymer in the process of being converted to char.
Department of Fire Protection Engineering assistant professor Stanislav I. Stoliarov received a 5-year, $412,000 NSF CAREER Award for his proposal to quantitatively model how polymers produce char, the insulating layer of carbon that forms on the surface of an object as it burns. Applied to the design of flame-resistant materials, the model could improve safety while reducing development costs and the need for brominated flame-retardants (BFRs).
Synthetic polymers, often in the form of plastic, are all around us, in almost everything we use, wear, play with, build with, and drive. Many of these plastics are derived from petroleum, which makes them highly flammable. BFRs are often used to counteract their flammability, but concerns have been raised that the additives could have a negative impact on the environment and human health. Better polymer design could reduce or eliminate the need for BFRs, and the way to do that, Stoliarov believes, is to improve how they char.
Burning a marshmallow is an easy way to observe the formation and effect of char. Once ignited, the marshmallow swells, bubbles and blackens. The char becomes a natural thermal energy barrier. When it covers most or all of the marshmallow’s surface, the flame goes out, leaving the inside gooey, but not burnt. Removing the char or pulling the marshmallow apart reveals pockets of air inside. The size, position, and density of these voids, called cells, affect how heat flows through a material, which in turn affects how the char is formed. An effective layer of char, which slows polymer degradation and reduces the burn rate, is a key factor in designing safer materials.
A simple demonstration of char formation using a marshmallow.
Currently, not much is known about char growth dynamics, in part because char and cell formation vary widely among polymers. There are no established methods of quantifying its ability to insulate or its morphology, and no accepted models that relate its structure to heat transfer. This makes the development of flame-resistant materials an expensive, inefficient process that often relies on trial and error.
Stoliarov believes that establishing a three-dimensional, transient, multiphysics numerical model for char will enable industry to fine-tune materials for the right balance of safety, cost, and mechanical properties. To obtain data for the model, he and his team are conducting an array of experiments that allow them to precisely record the effects of heat on the physical and chemical properties of polymers.
In a process called controlled condition pyrolysis, polymer samples are placed in a chamber with an inert atmosphere, and then gradually heated to high temperatures. This causes thermal degradation without starting a fire. Like the marshmallow, the polymer swells, sometimes to many times its original height. The char it produces is so fragile it crumbles if touched, so during and after the process Stoliarov’s team uses non-intrusive temperature monitoring to record heat transfer, and high-resolution X-ray tomography to obtain cross-section images of the char and its cells. The team is currently testing both well-known materials like PVC, and emerging materials such as biodegradable plastics.
The results aren’t always obvious. For example, a larger or denser layer of char may not protect a polymer as well as a smaller or airier one. For this reason, Stoliarov believes the answers lie not in the char alone, but also in the cells.
“The question remains,” says Stoliarov, “what are the exact mechanisms and dynamics inside? One of the key goals of my career is to connect the dots in a quantitative fashion.”
Published July 15, 2014